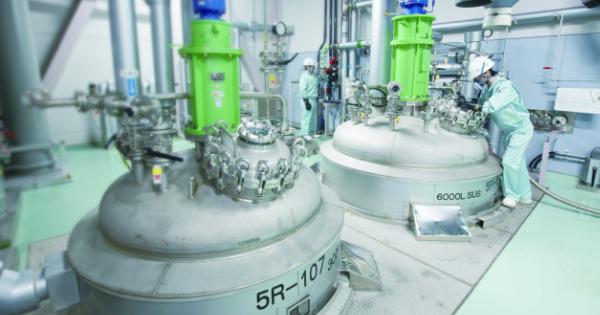
Fuji Chemical Industries manufactures more than 1,000 tons of APIs annually, and provides GMP contract services to domestic and overseas clients. centered on the GMP process from intermediates to APIs to domestic and overseas pharmaceutical manufacturers.
Contract manufacturing is carried out in Organic Building No.1, No.2, No.5 and test buildings, which are all multipurpose plants and cGMP compliant. In addition to 75-9,000L reactors, we also have a reactor that can support cryogenic reaction along with autoclaves up to 6,000L.
refining facility equipped with a class 100,000 clean room for API manufacturing, and depending on the production volume, we can provide three systems of equipment that support scales of 300L to 6,000L.
We can serve you with a small-quantity trial to commercial production for various types of reactions.
Features of our services
- Various cGMP multi-purpose facilities
We have a total of 47 reactors ranging from 75 to 9,000L liters
(GMP glass lining reactors from 20L) - 3 systems of refinery (Class 100,000)
Crystalizers ranging from 300 liters and 6000 litters - Large size dryers and centrifuges
2000L Nauta dryer, 5000L double-corn dryer, and 24-inch Heinkel. - Pilot equipment
Smoothe transfer from a pilot to commercial scale - Capable of handling special reactions (cryogenic, Raney Ni, etc.)
Equipment handling Cryogenic (–80 ℃) and hydrogenation (0.8MPa)
Hydrogenation and cryogenic reaction
- Reactor size
- 300L (HASTELLOY) and 1500(GL) - Hydrogenation under acidic condition feasible
- MAXBLEND® type impellers
- Excellent dispersion and circulation supports hydrogenation - Supports reactions under pressure up to 0.8 MPa and under acidic conditions. We have a track record of hydrogenation reactions using various catalysts such as Pd / C, Rh / C, and RaineyNi.
- Cryogenic reactions under the temperatures down to -80 C°. Has much experience in cryogenic reactions using BuLi.
Reaction examples
Type | Reaction name |
Alkylation | Suzuki-Miyaura Coupling; Wittig reaction; Friedel-Crafts reaction; Grignard reaction; Michael addition reaction |
Halogenation | Bromination; iodination; fluorination (NaF; KF); chlorination |
Oxidation reaction | Peroxide oxidation; Swern oxidation; SO₃•Py oxidation; TEMPO oxidation |
Reduction reaction | Catalytic hydrogenation (Pd, Rh, Ni); Wolff-Kishner reduction; NaBH₄ reduction; BH₃ reduction; hydrazine reduction; Vitride reduction |
Cryogenic reaction | Aldol addition via lithiation using lithium alkyllithium (n-BuLi) or LDA., bromination, and borylation |
Amidation reaction (peptide synthesis) |
Reactions using various condensing agents such as mixed acid anhydride method and water soluble carbodiimide |
Sulfidation | Reactions using mercaptan and thiophenol |
Other | Chlorosulfonation reactions of aromatics with chlorosulfonic acids; formylation reactions; optical resolution; Reformatsky reactions; Buchwald-Hartwig reactions; Mitsunobu reactions |
Facility Overview
Organic Building No.1
A multipurpose plant inspected by FDA. It has 4,000 to 6,000 liter reactors and large scale manufacturing. In addition, it is fully equipped with a clean room and able to perform refinery of investigational drugs.
Reactor size | No. of reactors | Centrifuge | Dryer |
600-6,000L | 14 | 7 | 1 |
Organic Building No.2
A FDA -inspected multipurpose plant. It has 2,000 to 3,000 liter main reactors and carry out medium-size manufacturing.
Reactor size | No. of reactors | Centrifuge |
100-5,000L | 13 | 4 |
Organic Building No.5.
The manufacturing facility built in 2007 is designed to completely prevent cross-contamination. A 2,000-9,000 liter reactors are installed to support mass production.
Reactors | No. of reactors | Centrifuges | Dryers |
2,000-9,000L | 7 | 2 | 3 |
Drying
FDA inspected facility for drying crystals. Each room is completely separated to prevent cross-contamination. There is also a clean room for drying APIs
Dryers |
4 |
Reactor size | No. of reactors | Centrifuges | Dryers |
75-1,500L | 9 | 3 | 2 |
Refinery Building
Equipped with a class 100,000 clean room, it supports the purification process of the final drug substance. It is equipped with one of the largest crystallizers (6,000L), and it also manufacture APIs for injections.
Reactor size | No. of reactors | Centrifuges | Dryers |
300-6,000L | 5 | 2 | 3 |
Mills/Pulverizer
Model | Material | Specification |
Roundel Mill (Grinding machine) |
Stainless steel | 50-500kg/h |
Atomizer (Pulverizer) |
Stainless steel | 50-150kg/h |
Turbo Screener (Vibrating Sieve) |
Stainless steel | 100-500kg/h |